一、 前言:
随着电子产品迅速向高频化、高速数字化、便携化和多功能化的发展,对电路板基板的线粗、线隙要求也越来越小,而业界仍基本采用经过图形电镀加工的方法生产基板,因而星点渗镀导致线中间线隙变小甚至短路的问题也普遍存在,星点渗镀的特点是板面不定位,分布无规律,时有时无,难以捉摸。此不仅影响了基板的外观而且可能会影响插件后电子产品的电气性能。本文就星点渗镀问题进行探讨。
二、 要因图分析:
造成星点渗镀问题的原因多种多样,除图电拉存在的问题外,干膜工序也会存在关联,以下是造成星点渗镀的鱼骨图:
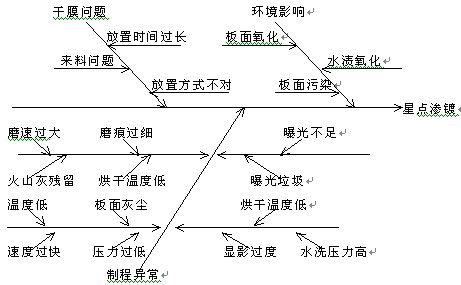
三、 试验内容:
针对上述原因分析,干膜质量导致的渗镀在以往的生产中已发生过,与本次的现象不同,故排除干膜本身的原因。以下就环境影响、制程参数方向进行仿真试验。
1. 磨板后水氧化试验。
2. 板面残留火山灰试验。
3. 快速磨板试验。
4. 板面油污试验。
5. 辘板条件变动试验。
6. 板面污染氧化试验。
7. 板面强烈氧化试验。
1. 磨板后水氧化试验:
2. 板面残留火山灰试验:
3. 快速磨板试验:
结果:未能模拟出星点渗镀,虽然速度加快1倍,但由于板面磨板前并未受到严重的污染(如油渍、严重氧化等),经贴膜后可抵抗图电药水的攻击,故并未发生渗镀现象。
4. 板面油污试验:
5. 辘板条件变动试验:
6. 板面污染氧化试验:
7. 板面强烈氧化试验:
9. 重复试验7
1. 板面污染氧化试验是仿真现时生产环境及停放时间影响。电路板各种药水时不时飞溅到板面上,在干膜与铜面所接触之位置攻击,降低干膜与板面之附着力,从而导致电镀过程中形成渗镀。
2. 改变磨板及贴膜条件,所生产之渗镀情况则表明了干膜在前处理条件不够好之情况下容易发生与铜面附着力不足,导致干膜剥落,覆盖密着性不足等现象,在电镀时产生渗镀。这也反映了干膜内部单体分子量较大,温度略低时其粘度较大,使其流动性变差。
1. 干膜之流动性不佳,造成干膜与铜面之密着性不够,是导致电镀时渗镀原因之一。
2. 待电镀之板存放环境不佳,受到外来酸、碱或强氧化性药液之污染侵蚀,破坏了干膜本身结构,削弱了干膜与铜面之结合力,是电镀时会造成渗镀原因之一,而此点是经常被忽略的,经过改良停放环境后再无发生此星点渗镀问题,希望本文能给相关同行一点启发。